خرید فولاد ابزار گرمکار
فولاد گرم کار چیست ؟
اهمیت فولاد گرم کار و سردکار به مراتب فراتر از آن چیزی است که امروزه به صورت رایج شناخته شده است. در زندگی روزمره ی کنونی تقریبا تمامی اشیایی که به وسیله ی آن ها احاطه شده ایم و با آن ها مواجه می شویم ، با فولاد های ابزار گرمکار و فولاد ابزاری سردکار تهیه و ساخته شده اند.
شرکت آن یانگ چین از بزرگترین تولید کنندگان فولاد دنیاست.
گستره ی کاربرد فولاد ابزار گرم کار بسیار پهناور است و ابزارآلات تولید شده به این وسیله در عرصه های بسیار متنوعی به کار گرفته می شوند. فولادهای ابزار گرمکار همچنین انواع مختلفی دارند از جمله : فولاد 1.2714 ، فولاد 1.2344 ، فولاد 1.2365 ، فولاد 1.2343 ، فولاد 1.2713 ، فولاد 1.2606 و فولاد 1.2567 که هر کدام از این فولاد ابزارهای گرمکار کاربرد و مشخصات منحصر به فردی دارند.
فولاد های ابزار گرم کار شکل دهی گرم قطعات کاری ساخته شده از فلزات آهنی و غیر آهنی و مشتقات آن ها را در درجه حرارت های بالا میسر می سازند. این فولادها در فرآیندهایی همچون ریخته گری تحت فشار ، اکستروژن گرم و آهنگری سقوطی و همچنین در تولید لوله و شیشه ، به کار گرفته می شوند.
ابزارآلات و تجهیزات ساخته شده از فولادهای ابزار گرمکار نه تنها همواره در مجاورت درجه حرارت های بالا قرا دارند بلکه همچنین در معرض تغییرات و نوسانات بارهای حرارتی که در اثر تماس مداوم سطوح ابزار با مواد در حال پردازش می باشد، نیز قرار دارند.
این بارهای حرارتی گاها متغیر در ترکیب با نیروهای سایشی ناشی از خراش یا ضربه ، فولادهای ابزاری گرمکار را نیازمند الزامات بسیار ویژه ای می نماید. خواص کلیدی این فولادها عبارتند از: مقاومت تمپرینگ بالا ، استحکام دمایی ، مقاومت در برابر شوک های حرارتی ، تافنس در دمای بالا و مقاومت سایشی بهینه.
استفاده از فولاد های ابزار گرم کار با کیفیت بالا برای حصول اطمینان از درجه ی مطلوب بهره وری عملیاتی و کارایی بالا ضروری می باشد. در عمل فولاد ابزار گرم کار بوسیله ی ترکیب شیمیایی شان و فن آوری تولیدی مورد استفاده برای آ نها و نیز عملیات حرارتی پس از آن ، قابل تعریف می باشند.
به طور کلی فولاد های ابزار گرم کار از آلیاژهای مقدار متوسط و پرآلیاژ می باشند و اکثریت آن ها مقدار محتوای کربن نسبتا پایینی دارند. (0.25 – 0.6)%.
برای مشاهده قیمت فولاد گرم کار و خرید فولاد گرمکار می توانید با شماره های درج شده در سایت تماس بگیرید. در ادامه برای سهولت خرید شما تمام خواص و ویژگی های فولاد گرمکار را بررسی کرده ایم تا کمترین سوالی در زمینه خرید و فروش فولاد ابزار گرمکار برای شما باقی نماند.
خصوصیات فیزیکی و مکانیکی فولاد ابزار گرم کار
فولادهای ابزاری گرمکار بایستی در برگیرنده ی خصوصیات فیزیکی و مکانیکی زیر باشند:
- مقاومت در برابر تغییرات ناخواسته ی شکلی در دمای کاری
- مقاومت در برابر شوک های حرارتی
- مقاومت در برابر سایش در دمای کاری
- مقاومت در برابر تغییر شکل در حین عملیات حرارتی
- قابلیت ماشینکاری خوب در شرایط آنیل شده
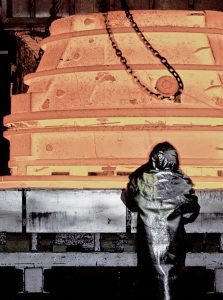
درحالیکه فرآیندهای مختلفی برای شکل دادن فلزات داغ همچون مهرزنی ، سوراخکاری ، کشش ، اکستروژن کردن ، غلطک کاری و چرخش وجود دارد . برای انجام موفقیت آمیز اینگونه فرآیندها در درجات حرارتی بالا ، ابزارآلات و تجهیزات بایستی ترکیبی از قدرت، مقاومت در برابر سایش و سختی را داشته باشند.
دمای عملیاتی به عنوان بالاترین درجه حرارتی که فولاد با آن مواجه می شود در نظر گرفته می شود . این دما همواره بالاتر از میانگین دمایی است که تجهیزات به آن رسیده اند. به عنوان مثال در ابزارآلاتی همچون قالب های فشاری و اکستروژن ، فلز در تماس مداوم با قالب برای مدت زمانی قابلی توجهی می باشد و بنابراین شدت حرارت در آن محل بسیار بالا می باشد . از طرف دیگر،در قالب های مهرزنی داغ تماس متناوب است و بر اثر اتلاف گرمایی و گرمازدایی ، گرایش به تعادل گرمایی وجود دارد.
برای تاب آوری در چنین شرایط سرویس دهی،مقاومت در برابر نرم شدگی حاصل از تمپرینگ و یا عملیات کشش و حفظ سختی در درجه حرارت های بالا از معیارهای ضروری فولادهای ابزار گرمکار هستند.
مقدار شوک حرارتی در حین سرویس دهی از اهمیت فوق العاده ای در تمامی فولادهای ابزاری گرمکار برخوردار می باشد. در فرآیندهایی همچون سوراخکاری ، هم دما بسیار بالاست و هم مدت زمان تماس بسیار طولانی می باشد . بنابراین برای جلوگیری از نرم شدگی در اثر آنیل شدن، سطح ابزار بایستی مابین هر دو عملیات به خوبی خنکشود . از آنجاییکه بالاترین میزان درجه حرارت در خارجی ترین لایه ی سطح می باشد ، این گرمایش و خنک شدن سیکلی و متناوب ،اثر انبساط و انقباضی بر لایه ی سطحی دارد . برای تاب آوردن در برابر چنین شرایطی ،فولاد بایستی از میزان بالایی از رسانش حرارتی برخوردار باشد. این شرایط که در شکل پایین به تصویر کشیده شده است، احتمالا یکی از رایج ترین مشکلات دردسرسازیست که یک فولاد ابزار گرم کار با ان مواجه می شود.
شرایط قالب فولادی گرمکار که نشان دهنده ی شرایط سخت تغییرات دمایی می باشد.
انواع فولاد ابزارهای گرمکار
فولادهای ابزار گرمکار رایج ، بسته به عناصر اصلی مورد استفاده در ساختار برای دستیابی به سختی ، به سه دسته تقسیم می شوند:
- فولادهای کروم دار
- فولادهای تنگستن دار
- فولادهای مولیبدن دار
طبقه بندی و ترکیبات شیمیایی انواع اصلی فولادهای ابزار
فولادهای ابزاری گرمکار کروم دار:
این گروه از فولادهای H10 تا H19 حاوی کروم می باشند.در مواردی از افزودن تنگستن ، مولیبدن،وانادیوم و کبالت استفاده می شود.در این گروه محتوای کربن نسبتا کم و در حدود (0.35 – 0.40)% نگه داشته می شود. این مقدار به همراه محتوای کم سایر عناصر آلیاژی کلی ، باعث افزایش تافنس در سختی طبیعی در حدود 400 تا 600 راکول سی می شود.
میزان کروم بالا در فولادهای این گروه به همراه کربن کم،سخت شدگی در عمق را تضمین می نماید . بنابراین این فولادها می توانند ضمن اینکه در هوا خنک می شونددر بخشی هایی با سطح مقطع 30 سانتیمتر هم به سختی کامل دست پیدا کنند.
مقدار بالای تنگستن و مولیبدن فولادهای H10 و H14 باعث افزایش سختی در درجه حرارت های بالا و استحکام گرمایی می شود.اما تمایل به اندکی کاهش در تافنس هم ایجاد می گردد.
در این گروه فولادهای H11,H12,H13 احتمالا بیشترین میزان استفاده را در میان تمامی فولادهای ابزاری گرمکار به خود اختصاص داده اند.
ویژگی های قابلیت سخت شدن در هوا و محتوای متعادل آلیازی مسئول اعوجاج کم در حین سخت شدن می باشند.
این فولادها برای انواع قالب های داغ ، از هر نوع ، بصورت ویژه بسیار مناسب می باشند. بویژه برای قالب های اکستروژن فلزات سفید و قالب های ریختگری تحت فشار و قالب های آهنگری و تیغه های برشی گرم بسیار سازگار می باشند.
مزیت عمده ی فولادهای این گروه را می توان توانایی مقاومت در برابر افزایش پیوسته ی دما تا میزان 540 درجه سانتیگراد دانست. این فولادها در عین حال ابزارالات سخت و هدایت کننده ی گرما را با استحکام کششی در حد 5مگاپاسکال در این دما ارائه می دهند.
فولاد H10 عضو تازه وارد این خانواده است.اولین بار در ایالت متحده معرفی شده است و در حال حاضر نیز در اروپا استفاده می شود.این فولاد نسبت به بقیه ی اعضای گروه تافنس بهتری دارد و کاربردهای بسیار مهمی را به خود اختصاص داده است.بسیاری از سازندگان فولاد برای دستیابی به طیف وسیعی از خواص مطلوب و مورد نظرشان با استفاده از ارکیبات شیمیایی فولاد H10 دست به ایجاد تغییراتی در بازار زده اند.
فولادهای ابزار گرمکار آلیاژ شده با تنگستن:
عناصر اصلی آلیاژی در این گروه از فولادها عبارتند از کربن،تنگستن و کروم . در مواقع خاصی وانادیوم نیز به آن اضافه می گردد. محتوای بالای عناصر آلیاژی باعث افزایش مقاومت به نرم شدگی در دماهای بالا در مقایسه با مقایسه با فولادهای کروم دار ساده ، شده است. اما فولادهای ابزار گرمکار این گروه شکننده تر می باشند.مقدار سختی کاری طبیعی فولادهای این گروه در حیطه ی 450 – 600 راکول سی می باشد.
در مقایسه با فولادهای ابزار گرمکار کروم دار،محتوای بالای تنگستن این فولادها را برای خنک شدن بوسیله ی آب در حین سرویس دهی نامناسب می سازد.
چنانچه ترکیبات شیمیایی فولادها را در این گروه بررسی نماییم در میابیم که به فولادهای تندبر شباهت دارند . در واقع نوع H26 نسخه ی کم کربن فولاد ابزار تندبر T1 می باشد.
در فولاد های ابزار گرمکار این گروه به طور کلی با کاهش محتوای کربن ، تافنس و مقاومت به شوک های حرارتی بالا می رود . با این حال لازم است که محتوای تنگستن و وانادیوم نیز تنظیم شود زیرا هر دو این عناصر با نگاه داشتن کربن اضافی در کاربیدهای پیچیده و بنابراین کربن کم ناکافی در ساختار آستنیت ، سبب کاهش سختی پذیری می شوند. به این ترتیب ترکیب شیمیایی تنظیم شده ، ترکیبی بهینه را از سختی و سختی در دمای بالا را به همراه میزان قابل توجهی از تافنس (چقرمگی) و مقاومت در برابر شوک حرارتی به نمایش می گذارد.
فولادهای ابزار گرمکار مولیبدن دار:
عناصر مورد استفاده در فولادهای ابزار گرمکار متعلق به این گروه عبارتند از مولیبدن ، وانادیوم ،تنگستن و مقادیر متفاوتی از کربن. درست مثل فولادهای ابزاری تندبر، فولادهای ابزاری گرمکار مولیبدن دار با انواع مربوطه ی تنگستن دار خود ، خواص و کاربردهای یکسانی دارند.
مزیت اصلی این گروه از فولادها نسبت به گروه قبل مقاومت بیشتر نسبت به تغییرات دمایی می باشد.
نکته ی قابل ملاحظه در خرید و فروش فولاد گرم کار این است که فولادهای این گروه نسبت به سایرین برای ممانعت از تخلیه ی کربن ،در هنگام عملیات حرارتی به مراقبت ها و توجهات بیشتری نیاز دارند.
جهت بالاترین بارها و تنش های حرارتی:
به عنوان یک تولیدکننده ی پیش رو در سراسر دنیا ، شرکت فولادسازی بوهلر تمام تمرکز خود را بر روی حل مشکلات مورد مواجهه مشتریان خود در هنگام ساخت و تولید ابزارالات و تجهیزات متمرکز ساخته است. از مهمترین این الویت ها فولادهای ابزاری گرمکار می باشند.
فولادهای ابزاری گرمکار فولاد های آلیازی می باشند که برای سرویس دهی در دماهای عمدتا بالای 200 درجه ی سانتیگراد طراحی شده اند.
در طول استفاده ابزار و تجهیزات ساخته شده از این فولادها به طور مداوم در تماس با مواد داغ قرار دارند.این دما بالای 200 درجه می باشد در ضمن به علاوه ی این بار حرارتی طولانی مدت،تنش های دیگری نیز به علت تغییرات مداوم درجه ی حرارت، بر فولاد وارد می گردد.
فولادهای ابزار جهت استفاده در چنین کارکردهایی باید قادر باشند که نه تنها در برابر تنش های مکانیکی و سایشی معمول که بر فولادهای ابزار وارد می آید مقاومت کنند بلکه آنها همچنین بایستی قابلیت ایستادگی در برابر انواع بارهای حرارتی را نیز داشته باشند.
ترکیبی بهینه از خصوصیات مکانیکی و همچنین متالورژیکی این امکان را فراهم می آورد که:
در روند تولید فولاد ابزار | در جریان استفاده از آن |
ماشینکاری آسان و قابلیت ماشینکاری فوق العاده
|
طول عمر بالا و یکنواخت قطعه
حداکثر ایمنی در برابر تخریب و شکست |
عملیات حرارتی ایمن و ساده
| |
ثبات ابعادی بالا در طول عملیات حرارتی
|
از تولید تا توزیع فولاد ابزار گرم کار :
مزیت ها | تعریف | ویژگی |
درسطح مقطع ها و لبه های تجهیزاتی که لایه برداری های عمیقی انجام می دهند، افزایش تنش های مکانیکی با شدت بالا می تواند منجر به ایجاد ترک های حرارتی شود. بنابرای زیاد بودن تافنس فولادها می تواند منجر به کاهش ریسک تشکیل ترک شود. بنابراین تافنس حرارتی را می توان به عنوان عامل مقاومت کننده در برابر شکل گیری ترک به شمار آورد. |
مقاومت ماده در برابر تشکیل و رشد ترک – تافنس فولادهای ابزار گرمکار با افزایش دما زیاد می شود. |
تافنس در دمای بالا |
با وجود استحکام کافی حتی در دماهای بالا،امنیت در برابر تغییر شکل ابزارآلات و تجهیزات افزایش می یابد. | توانایی یک ماده در جذب تنش بدون تغییر شک را گویند. اگر ریز ساختار یک ماده در دمای زیاد تغییر کند،استحکام آن در دمای اتاق و متعاقبا استحکام ان در دمای بالا کاهش خواهد یافت. |
استحکام حرارتی |
با وجود ویژگی مقاومت به تمپرینگ، میزان سختی فولاد گرم کار در حد مورد نیاز در حین کار در درجه حرارت های بالا تضمین خواهد شد. | مقاومت ماده در برابر نرم شدگی در درجه حرارت های بالا را می گویند. |
قابلیت حفظ سختی در دماهای بالا |
با داشتن مقاومت در برابر سایش به قدر کفایت در درجه حرارت های بالا، ریسک فرسایش و ساییدگی کاهش پیدا می کند. | مقاومت در برابر از دست دادن ذرات سطحی بر اثر عوامل مکانیکی خارجی را گویند. | مقاومت در برابر سایش در درجه حرارت های بالا |
شکل گیری و گسترش ترک های حرارتی شبکه ای تشکیل شده روی سطح که ناشی از تغییرات دمایی می باشند به تعویق می افتند. | توانایی یک ماه در برابر بارهای متناوب که در اثر تغییرات مداوم درجه حرارت بوجود می آید. |
مقاومت در برابر شوک های حرارتی |
از یک طرف با وجود رسانایی بالای حرارتی شیب گرمایی که منجر به تنش های حرارتی می شود کاهش پیدا می کند و از طرف دیگر میزان گرمای آسیب رسان به دور از لایه ی سطحی منتقل می گردد.وجود این خاصیت منجر به کاهش دفرگی و تغییر شکل و ترک های حرارتی و بدشکل می شود. | سرعت توزیع و پخش شدن انرژی گرمایی از یک نقطه تا سراسر ماده را گویند. |
رسانایی حرارتی |
بایستی در نظر گرفت که این خصوصیات بوسیله ی خصوصیات متالورژیکی فولاد تعیین می گردند و بنابراین در طول فرآیند ذوب فولاد های ابزار گرم کار ،تنظیم می گردند. تجربیات و تحقیقات جاری منجر به پیشرفت فزاینده ی این ویژگی های متالورژیکی از طریق بهبود فرآیندهای ذوب و ذوب مجدد، شده است.
نمودار تغییرات تافنس بر حسب ذوب مجدد در انواع فولادهای بوهلر
نمودار ارتباط درجه ی خلوص و کیفیت فولادهای ابزاری بوهلر
مقایسه ای در خواص فولادها:
مقایسه ی کیفی در خصوصیات عمده ی فولادها
این جدول برای سهولت در انتخاب فولادها گردآوری شده است.اما به هرحال بایستی در نظر داشت که دربرگیرنده ی اطلاعات و شرایط متفاوت باری که متاثر از کارکردهای گوناگون است، نمی باشد.
مقایسه ی بین خصوصیات مکانیکی برخی از انواع فولادهای ابزار گرمکار
در جدول زیر ترکیبات شیمیایی برخی از فولادهای ابزاری گرمکار آورده شده است:
ترکیب شیمیایی برخی از فولادهای ابزاری گرمکار
کاربردها:
کاربردها | فولاد بوهلر | |
ابزارآلات گرمکار که تحت تنش بالایی قرار دارند.همچون سنبه ها و قالب ها – محفظه های قاب و قالب های اکستروژن | در ابتدا تنها برای پردازش آلیاژهای فلزی سبک به کار گرفته می شده است. | W300
|
ابزارآلات و تجهیزات اکستروژن داغ – تجهیزات ریختگری تحت فشار (دایکست) – قالب های شکل دهی – تیغه های برشی داغ | W302 | |
تجهیزات ساخت قطعات توخالی – تجهیزات و ابزارآلات پیچ و مهره و پرچ | W303 | |
در ابتدا تنها برای پردازش آلیاژهای فلزی سنگین به کار گرفته می شده است. | W320 | |
در ابتدا تنها برای پردازش آلیاژهای فلزی سبک به کار گرفته می شده است. | W350 | |
قالب ها و پانچ های مورد استفاده در آهنگری گرم و داغ – تجهیزات پرسکاری با سرعت بالا – کاربردهای فولادهای ابزار سردکار که در آن ها تافنس ویژگی بسیار حیاتی به شمار می رود – تجهیزات اکستروژن – قالب های دایکست – کاربردهای خاص در قسمت های کار با پلاستیک ها | در ابتدا تنها برای پردازش آلیاژهای فلزی سبک و سنگین به کار گرفته می شده است. | W360 |
ابزارآلات و تجهیزات گرمکار که تحت تنش بسیار بالایی قرار دارند همچون سنبه ها و قالب ها – محفظه های قالب – قسمت لوله ای قالب های اکستروژن – تجهیزات دایکست – قالب های شکل دهی – تیغه های برش داغ – تجهیزات اکستروژن داغ – تجهیزات ساخت بدنه های توخالی – تجهیزات ساخت پیچ و مهره | در ابتدا تنها برای پردازش آلیاژهای فلزی سبک به کار گرفته می شده است. | W400 |
W403 | ||
فولادهای ابزار گرمکار و سردکار برای استفاده های طولانی مدت در دمای باای 450 درجه سانتیگراد – تجهیزات پرسکاری هیدرواستاتیکی- تجهیزات اکستروژن سرد – تجهیزات کنده کاری سرد – قالب های صنعت پلاستیک – تجهیزات دایکست برای آلیاژهای آلومینیوم و روی – تجهیزات پرسکاری گرم | W720 | |
تجهیزات و ابزار کنده کاری سرد – تجهیزات اکستروژن سرد – صفحات برشی – قالب های صنعت پلاستیک – تجهیزات دایکست برای الیاژهای آلومینیوم و روی – تجهیزات پرسکاری داغ | W722 |
ریختگری تحت فشار (دایکست)
در فرآیند ریختگری تحت فشار فلز مذاب به داخل قابی که دقیقا مشابه محصول نهایی است تزریق می گردد،سپس تحت فشار قرار می گیرد و جامد می گردد.مذاب هایی که میتوان بوسیله ی این پروسه به آن ها شکل داد شامل مواد با درجات ذوب پایین می گردند همچون آلیاژهای قلع و سرب . آلیاژهای با رنج متوسط نقطه ذوب هم قابلیت شکل گیری به وسیله ی این فرآیند را دارند. مانند آلومینیوم و آلیاژهایش و همچنین آلیاژهای مس با نقطه ذوب کمی بالاتر.
ریختگری تحت فشار نوعی ریختگری است که مواد مذاب تحت فشار به داخل قالب تزریق می گردند.در این سیستم بر خلاف روش های دیگر ریختگری که مذاب متاثر از نیروی وزن خود به داخل قالب می رود،مواد مذاب بوسیله ی یک نیروی فشاری داخل قالب تزریق می گردد و در همان حالت تحت فشار،منجمد می گردند و امکان تولید قطعات با استحکام بالا را فراهم میآورد.
ریختگری تحت فشار کوتاهترین راه تولید یک محصول از فلز می باشد. یکی از مزایای این روش تولید قطعات بسیار نازک و همچنین با استحکام بسیار زیاد می باشد که ساخت آن ها توسط روش های دیگر ریختگری تقریبا غیر ممکن است. در ریختگری تحت فشار، محفظه ی قالب در تماس مداوم با مذاب است .این محفظه در دمای ریختگری قرار می گیرد.
از آنجاییکه آلیاژهای آلومینیوم و مس با فولاد محفظه ی ریختگری واکنش نشان می دهند ، هرچه مدت زمان این تماس بیشتر باشد منجر به خوردگی و سایش بیشتر می شود .به همین علت اینگونه فلزات و آلیاژها تحت پروسه ی دایکست سرد قرار می گیرند. در این روش مذاب تحت فشار 200 – 300 bar قرار می گیرد ، به علت این فشار بالا این روند به سرعت اتفاق می افتد حتی اگر وزن و حجم آن ها بالا باشد،ظرف چند ثانیه پر می شود. امروزه بالغ بر 80% ریختگری آلومینیوم از طریق دایکست سرد انجام می گیرد.
هسته | قالب | پیستون | محفظه ی ریختگری | مشخصات مورد نیاز |
*** | *** | ** | **** | مقاومت سایشی |
***** | *** | ** | *** | ویژگی حفظ سختی |
*** | *** | * | ** | استحکام در دمای بالا |
***** | **** | * | ** | مقاومت حرارتی |
*** | ***** | ** | ** | تافنس در دمای بالا |
اکستروژن:
جهت انجام فرآیند اکستروژن ماده ی اولیه ی مورد نظر به درون قالب اکستروزن که سطح مقطع مورد نظر روی آن ایجاد شده است،فشرده می شود و در نتیجه قطعه اکسترود شده با سطح مقطع قالب تولید می گردد.مزیت این روش نسبت به دیگر فرآیندهای شکل دهی،قابلیت بالا در تولید قطعاتی با سطح مقطع پیچیده و همچنین شکل دهی مواد ترد و شکننده است زیرا ماده در این روش تنها تحت فشار و تنش برشی قرار می گیرد.اکستروزن می تواند پیوسته ( تولید قطعات با طول زیاد) یا نیمه پیوسته (تولید چند تکه ای) باشد . فرآیند اکستروزن میتواند بوسیله ی مواد اولیه ی سرد یا گرم انجام پذیرد.
اکستروژن مستقیم:
- ماده ی تغییر شکل یافته
- قالب بند
- قالب
- بیلت
- دامی
- محفظه
- میله ی پرس
اکستروژن مستقیم رایج ترین نوع اکستروژن است که در آن جهت حرکت پیستون و محصول اکستروژن یکسان می باشد. در حقیقت در این روش قالب ثابت می باشد و پیستون بیلت را به درون قالب حرکت می دهد.
اکستروژن غیر مستقیم:
- ماده ی تغییر شکل یافته
- دامی
- بیلت
- توپی درزگیر
- محفظه
- میله ی پرس
در اکستروژن غیر مستقیم،جهت حرکت پیستون و محصول اکستروژن، مخالف یکدیگر هستند. در این روش بیلت و محفظه ای که در بیلت داخل ان قرار دارد، با یکدیگر به سمت قالب که ثابت است حرکت می کنند. به دلیل اینکه در این روش بیلت و محفظه با یکدیگر حرکت می کنند ، نیروهای اصطکاکی بین آن ها کاهش پیدا می کند.
اکستروژن هیدرواستاتیک:
- ماده ی تغییر شکل یافته
- قالب
- درزگیر
- بیلت
- محفظه
- میله ی پرس
- سیال روانکار
این روش نوین جزو زیرشاخه های اکستروزن می باشد که به سرد و گرم و داغ انجام می پذیرد. اولین استفاده ی صنعتی و کاربردی اکستروژن هیدرو استاتیک از سال 1983 میلادی شروع شده است. بااین وجود پیشرفت این روش به خصوص در تولید مواد نانوساختار در سال های اخیر انجام شده است.
روش انجام این فرآیند به این ترتیب است که یک بیلت (به صورت استوانه ای شکل) اولیه در داخل محفظه ی اکستروژن قرار می گیرد ، سپس توسط پیستون پرس فشار به یک سیال منتقل می شود و در نهایت فشار یکنواخت سیال موجب تغییر شکل و اکستروزن می گردد.
میله ی پرس | نگه دارنده ی لاینر | لاینر | پوشش | مشخصات مورد نیاز |
** | * | **** | * | مقاومت سایشی |
**** | *** | **** | *** | سختی فولاد گرم کار در دمای بالا |
*** | **** | **** | *** | استحکام دمای بالا |
* | ***** | *** | ***** | مقاومت خزشی |
* | * | **** | * | مقاومت حرارتی |
***** | *** | ** | * | استحکام فشاری |
** | * | *** | *** | تافنس در دمای بالا |
فرآیند آهنگری (فورجینگ)
آهنگری در تعریف عبارت است از شکل دهی غیر برشی فلزات بین دو ابزار. انتخاب فولاد ابزاری بوسیله ی نوع عملیات آهنگری مربوطه تعیین می گردد.
آهنگری سقوطی:
فرآیند آهنگری سقوطی فرآیندی است که در آن چکش بالا می رود و سپس بر روی قطعه ی کار سقوط می نماید تا به شکل قالب تغییر شکل دهد . در این پروسه تنش های مکانیکی بسیار بالا هستند بنابراین داشتن تافنس خوب برای فولاد ابزاری کارگرم مورد استفاده بسیار حائز اهمیت می باشد.
در مقایسه با این روش تماس ما بین قطعات در فرآیند اهنگری پرسی در بازه ی طولانی تری از زمان رخ می دهد که بنابراین سبب ایجاد تنش های بالاتری در ابزارالات و تجهیزات می گردد. از اینرو در چنین مواردی فولادهای ابزار گرمکار با پایه ی کروم – مولیبدن استفاده می گردند که مشخصه ی بارز ان ها خواص خوب مقاومت به تمپرینگ ف استحام در دمای بالا ف مقاومت سایشی در دمای بالا و تافنس در دمای بالای خوب می باشد.
آهنگری سریع:
این فرآیند یک پرس تمام اتوماتیک چند مرحله ای می باشد که قابلیت شکل دهی اشکال بسیار پیچیده را از موادی که حتی به سختی شکل می پذیرند، در چند مرحله ی تغییر شکل فراهم می اورد.
این تجهیزات اغلب برای تولید اجزای چرخشی متقارن مورد استفاده قرار می گیرند.
آهنگری نیمه گرم:
واژه ی آهنگری نیمه گرم به فرآیندی اشاره می نماید که در آن قطعه کاری پیشگرم می شود. در این روش ماده در دمایی زیر نقطه ی تبلور مجدد تغییر شکل می دهد. عملا برآورد شده است که در این روش محدوده ی دمایی تغییر شکل فولاد 650 – 950 درجه سانتیگراد میباشد که مشخصا پایین تر از حیطه ی دمایی رایج آهنگری فولاد (1100 – 1250) درجه سانتیگراد می باشد.
اهنگری نیمه گرم | آهنگری سقوطی با پرس | آهنگری سقوطی با چکش | مشخصات مورد نیاز |
***** | ***** | ***** | مقاومت سایشی |
*** | **** | ** | حفظ سختی در دمای بالا |
**** | *** | *** | استحکام در دمای بالا |
* | ** | * | مقاومت حرارتی |
** | *** | **** | تافنس در دمای بالا |
عملیات حرارتی:
امروزه عملیات حرارتی نه تنها برای دستیابی به سختی فولاد گرم کار مورد نظر مورد استفاده قرار می گیرد بلکه بر روی خصوصیات مکانیکی متعدد درگری نیز تاثیر گزار می باشد. خواصی همچون تافنس،مقاومت در برابر شوک های حرارتی.
از همین رو بسیار ضروریست که عملیات حرارتی فولادها را دقیقا مطابق جداول راهنما و دستورالعمل های همراه با محصولات، انجام دهیم.
این موضوع بویژه برای فولادهای ابزاری گرمکار از اهمیت ویژه ای برخوردار است . تجهیزات ساخته شده از این فولادها از نظر ابعادی بسیار بزرگ هستند که این امر عملیات حرارتی آنها را با مشکل مواجه می کند . عملیات حرارتی سخت سازی برای پرهیز از ایجاد ترک های ناخواسته ی حاصل از افزایش دما ، باید در حمام نمک و یا خلا انجام پذیرد ، این جریان به منظور امکان برقراری تعادل گرمایی بین هسته و سطح باید به آهستگی انجام پذیرد.
برای خرید فولاد ابزار گرمکار با کارشناسان ما در بانک فولاد در ارتباط باشید.
ابزار سازی:
نیتریده کردن فولاد گرم کار :
نیتریده کردن عبارت است از غنی سازی لایه ی سطحی ابزارآلات و تجهیزات بوسیله ی نیتروژن ، از طریق عملیات ترموشیمیایی در درجه حرارت تقریبی 500-580 درجه سانتیگراد.خارجی ترین لایه متشکل از ترکیبات نیتروژن دار می گردد که این لایه ی سخت مسئولیت میزان بالای مقاومت سایشی قطعه کاری را به عهده می گیرد.
درست به همین دلیل است که ابزار در معرض مقدار بالای نیروهای سایشی اغلب نیتریده می گردند. با این وجود بایستی در نظر داشت با نیتریده کردن مواد گرایش به کاهش تافنس دارند و علت این امر آن است که لایه ی سخت تشکیل شده به شدت ترد است و به آسانی ترک میزند و این ترک ها منتشر شده و به فولاد پایه ای منتقل می گردد.
به طور کلی برای به حداقل رساندن این مشکلات بایستی اجزاء از نظر شکلی پیچیده با سطح مقطع های متفاوت و ابعاد بزرگ بایستی به آهستگی گرم و سرد شوند.
به منظور اینکه قطعه کاری نیتریده شده از نظر حرارتی در حین عملیات نیتریده کردن باثبات بماند، بایستی که در ابتدا در دمایی بالاتر از دمای نیتریده کردن تمپر شود و به این ترتیب کلیه ی تنش های داخلی بوسیله ی تنش زدایی قبل از شروع عملیات نیتریده کردن حذف می شود.
تعمیرات و نگهداری در طول استفاده:
گرمادهی مجدد فولاد گرمکار :
حداکثر بهره وری یک ابزار تنها در صورتی حاصل می شود که اقدامات صحیح هم قبل از پیاده سازی تجهیزات و هم در حین استفاده ی آن انجام پذیرد.
به منظور کاهش تحریک حاصل از تنش های حرارتی براثر تماس با فلزات داغی که در حال پردازش می باشند و در نتیجه کاهش ترک ها ، قالب ها بایستی به دقت پیشگرم شوند. درجه حرارت پیش گرم کردن بستگی به دمای فلزاتی دارد که تحت پردازش قرار می گیرند.
پیش گرمایش قالب ها برای این منظور بایستی به آهستگی و در کل قالب انجام پذیرد.
تنش زدایی:
تنش های حاصل از تغییرات مداوم درجه ی حرارت و بارهای مکانیکی ، نیازمند آزادسازی در هر زمان بوسیله ی یک عملیات تمپرینگ مناسب، هستند. تجربیات فراوانی تایید کنندهی این مطلب هستند که تنش زدایی در حین کار باعث افزایش طول عمر قطعه می شود.
این عملیات تنش زدایی بایستی در سیکل های چندین ساعته و در دمای 30-50 درجه پایین تر از بالاترین دمای تمپرینگ انجام پذیرد. قطعات بایستی به دنبال آن به آهستگی در کوره خنک شود.
پس از جداسازی ابزارآلات و تجهیزات از محموله ها، تمیزکاری و تنش زدایی آن ها توصیه می گردد.
جوشکاری فولاد گرمکار :
جوشکاری را می توان مبحثی جدایی ناپذیر از فولادهای ابزاری گرمکار دانست.به طور کلی می توان گفت که هر دو گروه فولادهای ابزاری گرمکار آنیل شده و نیز آنهایی که قبلا سخت شده و تمپر شده اند ، جوش پذیرند.
قبل از جوشکاری فولاد گرمکار پیش گرمایش تا حداقل دمای 325 درجه ی سانتیگراد امری ضروریست. در طی جوشکاری نیز توجه به این نکته ضروری است که دما نباید پایین تر از این دما افت کند و نیز نباید بالاتر از 475 درجه سانتیگراد برود.
پس از اتمام پروسه ی جوشکاری فولاد گرمکار ، نرخ خنک کاری بسیار آهسته پیشنهاد می گردد. ماده ای که قبلا آنیل شده بایستی پس از جوشکاری مجددا آنیل گردد و تجهیزاتی گه قبلا سخت و تمپر شده اند بایستی به دمای 30 درجه پایین تر از آخرین دمای تمپرینگ رسانده شود.